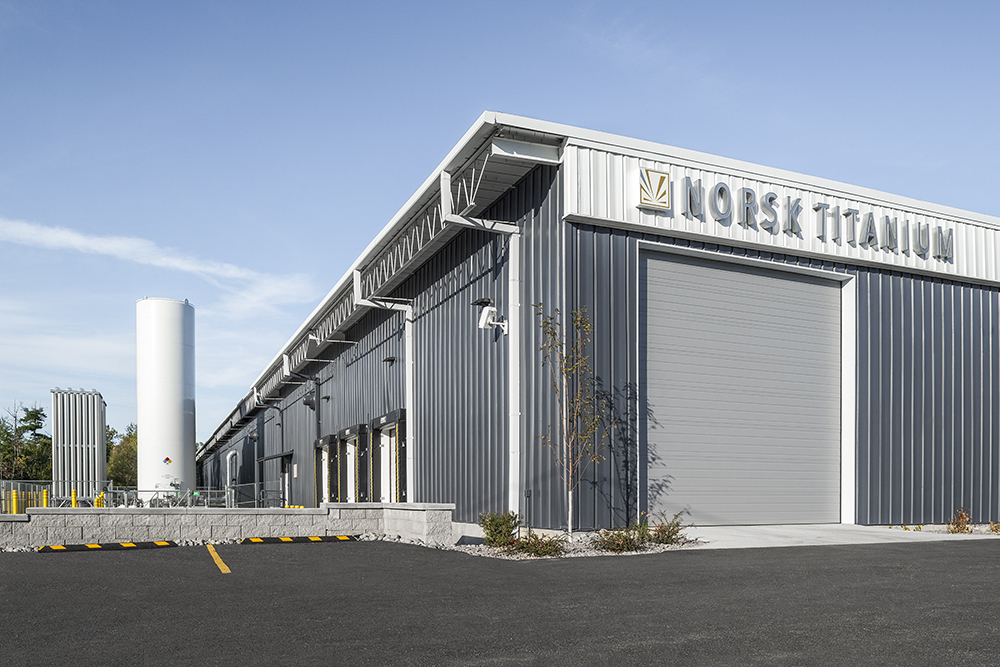
Norsk Titanium Marks Milestone in Additive Manufacturing
Additive Manufactured Integrally Bladed Rotor Enters Second Phase of Testing
Paris, France – June 18, 2019 – Officials with the University of Notre Dame Turbomachinery Laboratory (NDTL), Norsk Titanium (Norsk), Pratt & Whitney and TURBOCAM International announce the continuation of testing of an additively manufactured integrally bladed rotor (IBR). Building on initial testing completed in 2018, this next phase of testing examines the dynamic properties of the IBR. Manufactured using Norsk’s revolutionary Rapid Plasma Deposition™ (RPD™) process, the IBR was inspected to the same quality specifications used in Pratt & Whitney’s current turbomachinery components.
The tests are being conducted at NDTL’s world-class turbomachinery test facility in South Bend, Indiana. After completion of the initial testing, where the IBR met 100% of all design, speed and pressure ratio test points, the current test program looks at low and high cycle fatigue characteristics of the IBR. Testing will include multiple acceleration/deceleration cycles and investigate synchronous vibration effects on the additively manufactured blades.
The testing was preceded by a manufacturing qualities evaluation performed by TURBOCAM. The evaluation found no evidence of alpha case, or residual stress concentrations, that would cause distortions typically found in additive materials. Additionally, TURBOCAM confirmed Norsk’s RPD™ material was well-suited to traditional milling operations, and was as stable as Ti6-4 forgings.
The ultimate goal of this effort is to develop the manufacturing specifications needed to deliver the complex, heavily-loaded components for turbomachinery applications, while providing the cost and schedule savings that have been proven on Ti 6-4 airframe components.
“Successful completion of this testing will show that additive materials can be used in turbomachinery applications, and paves the way to a full qualification effort,” said Norsk’s Chief Commercial Officer Chet Fuller.
The entire manufacturing and testing effort has been overseen by Pratt & Whitney and is being evaluated for application to future engine developments.
“Pratt & Whitney is excited to enter this next phase of testing. Utilizing additive manufacturing techniques, such as Norsk’s Rapid Plasma Deposition process, allows us to shorten the manufacturing and development schedule for our critical turbomachinery components,” said Chris Kmetz, vice president of Engineering, Module Centers, Pratt & Whitney.
For more information on Norsk, visit www.norsktitanium.com. Norsk will also have a display of its RPD™ technology, and the first additive manufactured IBR, at the International Paris Airshow, June 17-20.